27.05.2022
Recently, the company applied the intelligent detection system to the hole-punching operation of transmission tower components for the first time, by building machine vision hardware equipment and corresponding supporting software on the automatic line of angle steel hole-punching.
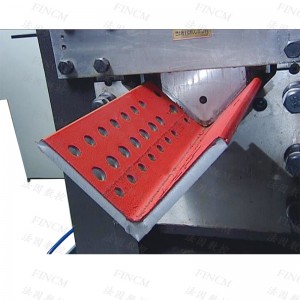
The system transmits and monitors relevant data and images in real time, implements online intelligent detection and diagnosis, escorts the quality of product processing, and helps realize "intelligent detection".
In recent years, with the continuous improvement of the quality of transmission tower components by customers, the amount of hole punching in the processing and production of iron tower components is very large.
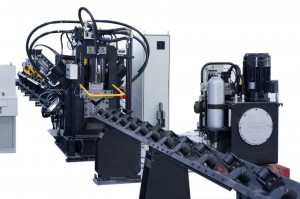
In order to ensure the processing size, position, quantity, etc. of the holes, it is necessary to arrange quality inspectors to conduct quality inspections during production.
However, the currently adopted manual sampling inspection method is affected by the objective conditions of the site and individual subjective factors, and is prone to misjudgment or missed inspection during the inspection process, and its instability, high labor intensity, low efficiency and high labor cost are not conducive to the realization of high Quality component inspection. This system can realize online monitoring, defect early warning and diagnosis by collecting and analyzing hole-punching process information.
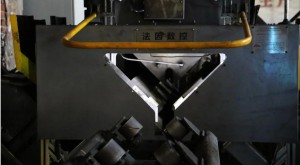
The system can realize real-time and rapid detection of key dimensions and quantities of holes made in tower components under working conditions, compare and discriminate the detection data with "standard" data, and alarm defects in time to ensure monitoring accuracy and efficiency. According to preliminary statistics, the online inspection system can meet the requirements of relevant standards for iron tower manufacturing. Compared with the traditional manual inspection method, its inspection accuracy can be improved by 10% or more, and the cost of defect rework or processing can be reduced by about 250,000 yuan per year every machine.
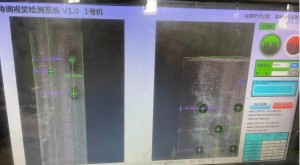
The company will continue to realize intelligent transformation and digital transformation efforts, in line with "new infrastructure" and new factory construction, and promote online inspection systems and production management systems.
Post time: May-27-2022